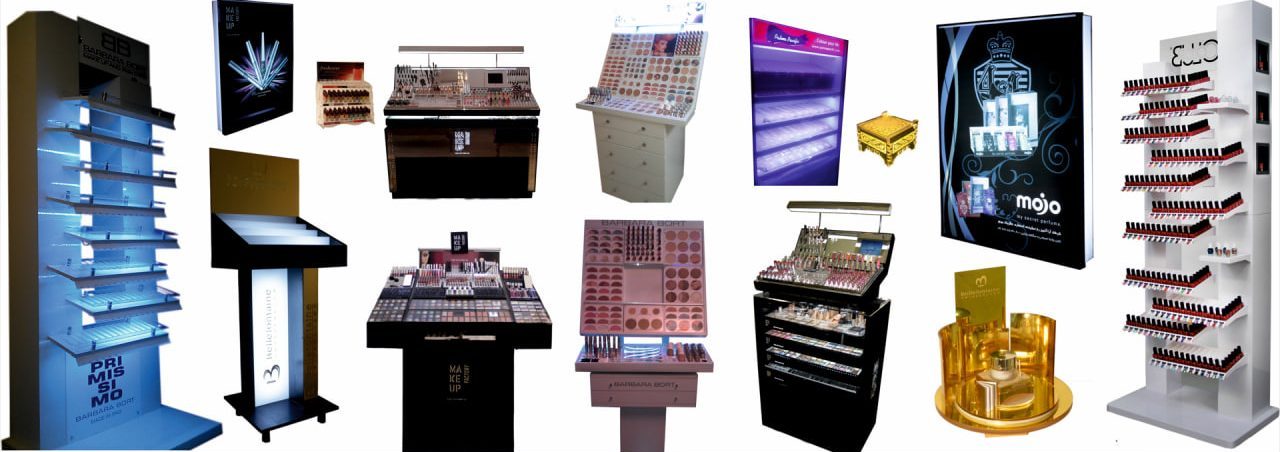
معرفی
درباره گلچین
در گلچین، هنر، دقت و خلاقیت را با فناوری پیشرفتهٔ لیزر ترکیب کرده ایم.
با تکیه بر نیم قرن تجربه در صنعت تبلیغات و دکوراسیون و ارائهٔ خدمات برش و حکاکی لیزری، پروژههای شما را از یک ایدهٔ ساده به اثری بینقص تبدیل میکنیم.
چرا گلچین؟
– ✅ تکنولوژی برتر: تجهیزات لیزری با قابلیت برش و حکاکی میکرونی روی پلکسی گلاس، چوب، فلز و سایر متریال.
– ✅ تیم متخصص: همکاری با مهندسان و طراحان مجرب برای اجرای پروژههای ساده تا پیچیده.
– ✅ گارانتی کیفیت: تضمین دقت ابعادی، پرداخت بی نقص و تحویل به موقع.
– ✅ مشاوره رایگان: همراهیتان میکنیم تا بهترین متریال، طراحی و روش اجرا را انتخاب کنید.
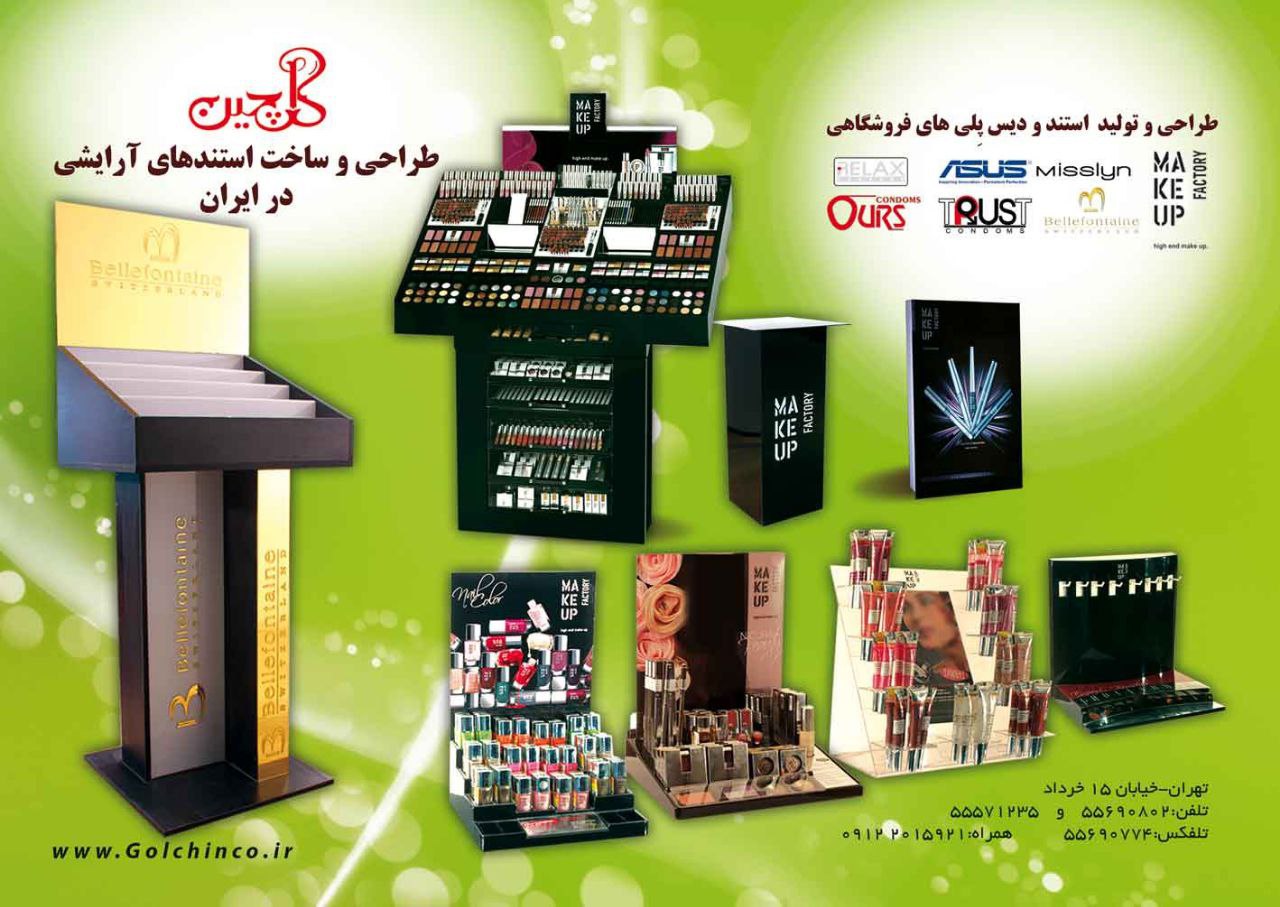
گــــــالری نمونه کارها
ماموریت ما این است:
– ارائهٔ راهکارهای سفارشی سازی شده برای نیازهای متنوع صنایع از تبلیغات و دکوراسیون تا قطعات صنعتی.
– حفظ بالاترین استانداردهای کیفیت و دقت با استفاده از دستگاه های لیزر مدرن و متریال نوین.
– تبدیل چالشهای پیچیدهٔ شما به فرصتهایی ملموس با تمرکز بر نوآوری و دوام.
قیمت و شرایط مناسب
مشاوره تلفنی
تضمین کیفیت
جهت ثبت سفارش و اجرای طرح های اختصاصی شماره خود را ثبت کنید
راههای ارتباطی با ما
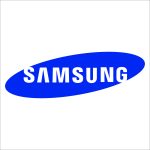
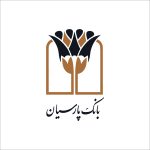
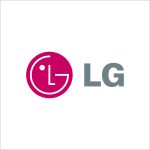
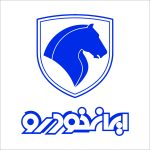
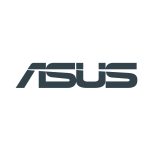
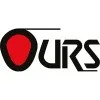
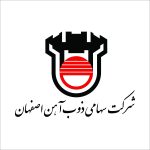
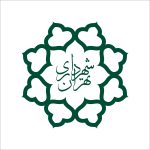
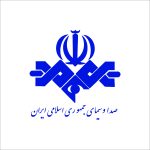
وبلاگ
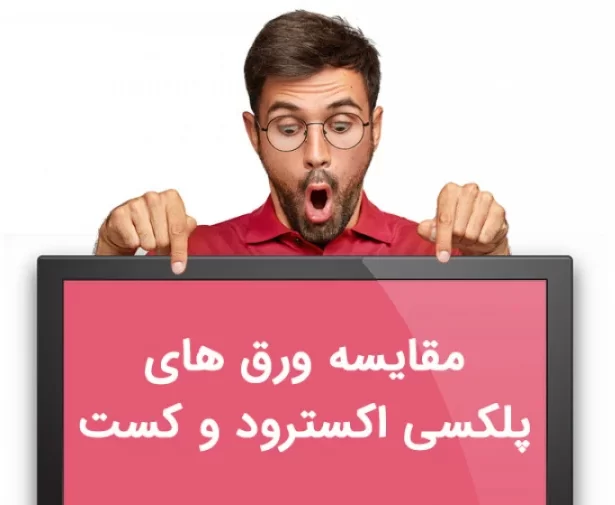
ورقهای پلکسی گلاس (اکریلیک) به دو روش اصلی اکستروژن (Extrusion) و کست (Casting) تولید میشوند. هر یک از این روشها ویژگیهای منحصر به فردی به محصول نهایی میبخشند که انتخاب بین آنها را به نیاز پروژه وابسته میکند. در این مقاله، تفاوتهای کلیدی این دو نوع ورق را بررسی میکنیم تا به شما در انتخاب مناسبترین گزینه کمک کنیم.
—
۱. فرآیند تولید: قلب تفاوت
الف. ورق اکسترود (Extruded Acrylic)
– روش تولید:
پلیمر PMMA ذوب شده و از طریق یک دستگاه اکسترودر با قالب تخت عبور داده میشود. پس از خروج از قالب، ورق با سرعت بالا خنک میشود.
– سرعت تولید: بالا (فرآیند مداوم).
– ضخامت: معمولاً نازکتر (تا ۶ میلیمتر).
ب. ورق کست (Cast Acrylic)
– روش تولید:
مونومر مایع MMA بین دو صفحه شیشهای ریخته شده و طی فرآیندی آهسته (چند روزه) در دمای کنترلشده پلیمریزه میشود.
– سرعت تولید: پایین (فرآیند ناپیوسته).
– ضخامت: امکان تولید ورقهای بسیار ضخیم (تا ۱۰۰ میلیمتر).
—
۲. مقایسه ویژگیهای کلیدی
ویژگی | ورق اکسترود | ورق کست |
---|---|---|
شفافیت | خوب | عالی (نزدیک به شیشه) |
مقاومت در برابر ترک | متوسط | بسیار بالا |
مقاومت شیمیایی | حساس به برخی حلالها | مقاومت بالاتر |
ضخامت | نازک (تا ۶ میلیمتر) | ضخیم (تا ۱۰۰ میلیمتر) |
هزینه | مقرونبهصرفه | گرانتر |
پرداخت سطح | احتمال خطوط ناشی از اکستروژن | سطح یکنواخت و صاف |
مقاومت حرارتی | تحمل دمای تا ~۷۰ درجه سانتیگراد | تحمل دمای تا ~۹۰ درجه سانتیگراد |
کاربرد در ماشینکاری | احتمال ترک خوردگی در برش | مناسب برای برش و حکاکی دقیق |
—
۳. تفاوت در کاربردها
ورق اکسترود: مناسب برای مصارف عمومی
– تابلوهای تبلیغاتی (حروف برجسته، استندها).
– پوشش نورپردازی (به دلیل قابلیت خمش حرارتی آسان).
– محصولات با تیراژ بالا (به دلیل هزینه پایین).
– کاربردهای سبک صنعتی مانند پنلهای محافظ.
ورق کست: ایدهآل برای پروژههای حرفهای
– آکواریومها و ویترینهای لوکس (شفافیت بالا و مقاومت در برابر فشار آب).
– ساخت ماکتهای دقیق (قابلیت ماشینکاری عالی).
– قطعات صنعتی پراسترس (مقاومت در برابر ضربه و ترک).
– کاربردهای هنری مانند مجسمههای شفاف.
—
۴. مزایا و معایب هر روش
ورق اکسترود
– ✅ مزایا:
– قیمت پایینتر.
– تولید سریع و انبوه.
– مناسب برای خمکاری با حرارت.
– ❌ معایب:
– شفافیت کمتر نسبت به ورق کست.
– مقاومت پایینتر در برابر مواد شیمیایی.
ورق کست
– ✅ مزایا:
– شفافیت استثنایی و سطح صیقلی.
– مقاومت بالا در برابر ترک، ضربه و مواد شیمیایی.
– امکان تولید ضخامتهای بسیار بالا.
– ❌ معایب:
– هزینه تولید بالا.
– زمان تولید طولانیتر.
—
۵. کدام را انتخاب کنیم؟ راهنمای سریع!
– ورق اکسترود مناسب است اگر:
– بودجه محدودی دارید.
– پروژه شما نیاز به ضخامت کم و تولید انبوه دارد.
– کاربردهای عمومی مانند تبلیغات یا نورپردازی مد نظر است.
– ورق کست انتخاب بهتری است اگر:
– به کیفیت نوری فوقالعاده نیاز دارید (مثلاً در ویترینهای لوکس).
– قطعه مورد نظر تحت فشار مکانیکی یا حرارتی بالایی قرار میگیرد.
– پروژه شما نیاز به ماشینکاری دقیق (مثل حکاکی لیزری) دارد.
۶. جمعبندی: علم انتخاب مواد
ورقهای اکسترود و کست هر دو از جنس پلکسی گلاس هستند، اما تفاوت در روش تولید، کاربردهای آنها را کاملاً متمایز میکند. درک این تفاوتها به شما کمک میکند تا با توجه به نیاز پروژه، بودجه و الزامات فنی، بهترین گزینه را انتخاب کنید.
اگر هنوز در انتخاب نوع ورق برای پروژهٔ خود مردد هستید یا نیاز به مشاوره فنی دارید، لطفا با ما تماس بگیرید.
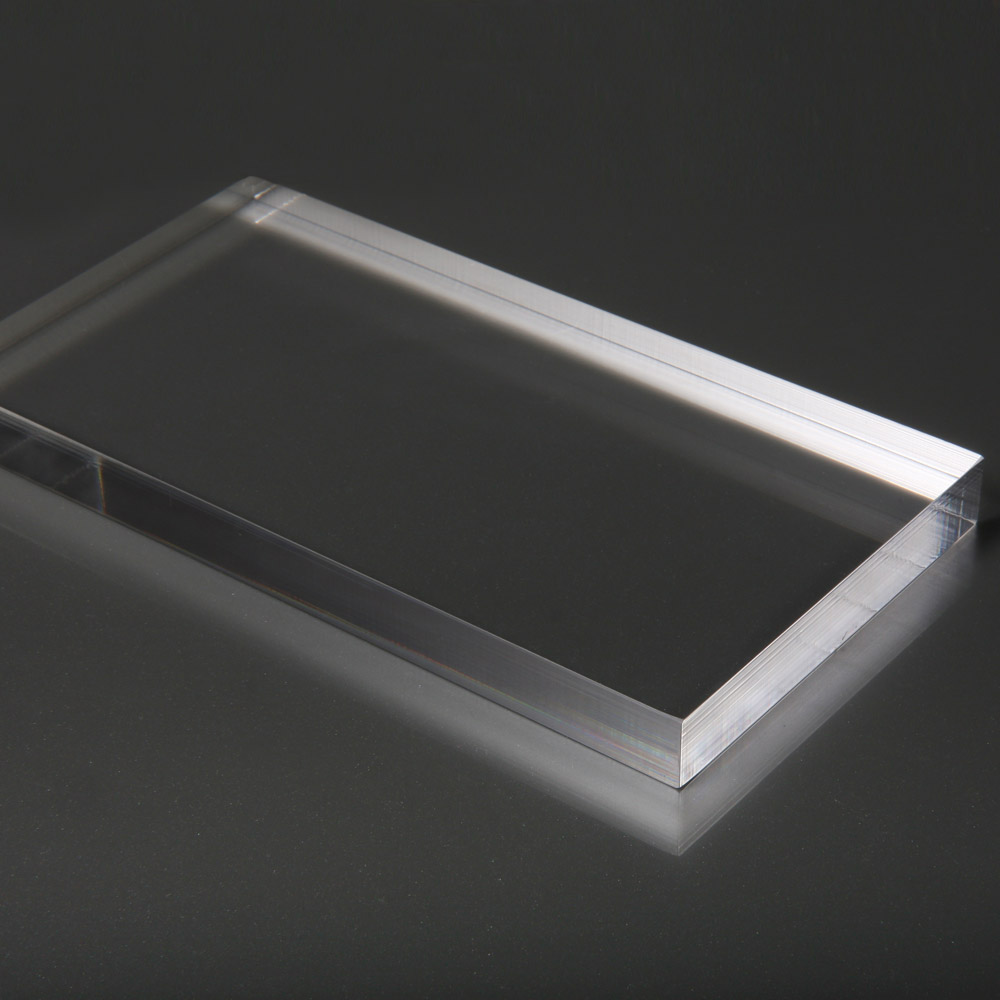
ورقهای پلکسی گلاس (اکریلیک) به دلیل شفافیت، مقاومت و انعطافپذیری، در صنایع مختلفی مانند تبلیغات، خودروسازی و ساخت قطعات صنعتی کاربرد دارند. تولید این ورقها فرآیندی دقیق و علمی است که در ادامه مراحل اصلی آن را بررسی میکنیم:
—
۱. مواد اولیه: پایه شیمیایی پلکسی گلاس**
پلکسی گلاس از پلیمری به نام پلی متیل متاکریلات (PMMA) ساخته میشود. ماده اولیه اصلی آن مونومر متیل متاکریلات (MMA) است که طی فرآیند پلیمریزاسیون به زنجیرههای بلند پلیمری تبدیل میشود. این فرآیند معمولاً با افزودن کاتالیزورها و مواد پایدارکننده برای کنترل واکنش شیمیایی همراه است.
—
۲. روشهای تولید ورق پلکسی گلاس**
تولید ورقهای اکریلیک به دو روش اصلی انجام میشود:
الف. روش اکستروژن (Extrusion)
– مرحله ۱: پلیمریزاسیون
مونومر MMA ابتدا در رآکتورهای شیمیایی تحت حرارت و فشار کنترلشده به PMMA تبدیل میشود.
– مرحله ۲: اکستروژن
پلیمر مذاب از طریق دستگاه اکسترودر (با قالبی تخت) عبور داده میشود تا به شکل ورق درآید.
– مرحله ۳: خنکسازی
ورق خروجی از اکسترودر به سرعت با آب یا هوا خنک میشود تا شکل ثابت خود را حفظ کند.
– مزایا: سرعت تولید بالا، هزینه کمتر، مناسب برای ورقهای نازک (تا ۶ میلیمتر).
ب. روش ریختهگری (Casting)
– مرحله ۱: آماده سازی مخلوط
مونومر MMA با افزودنیهایی مانند رنگدانه یا مواد ضد UV مخلوط شده و بین دو صفحه شیشه ای (قالب) ریخته میشود.
– مرحله ۲: پلیمریزاسیون آهسته
قالبها در اتاقکهای حرارتی قرار میگیرند تا مونومر به آرامی به PMMA تبدیل شود (این فرآیند ممکن است چند روز طول بکشد).
– مرحله ۳: جدا کردن ورق
پس از سخت شدن کامل، ورق از قالب شیشه ای جدا شده و لبههای آن پرداخت میشود.
– مزایا: کیفیت نوری عالی، مقاومت بیشتر در برابر ترک خوردگی، امکان تولید ورقهای ضخیم (تا ۱۰۰ میلیمتر).
—
۳. پرداخت نهایی
پس از تولید، ورقهای پلکسی گلاس مراحل زیر را طی میکنند:
– برش: ورقها با دستگاههای CNC یا لیزر به ابعاد دلخواه برش میخورند.
– پولیش: سطح ورق با مواد شیمیایی یا حرارت صیقل داده میشود تا شفافیت و جلای بهتری پیدا کند.
– پوششهای ویژه: برخی ورقها با لایههای ضدخش یا ضد UV پوشانده میشوند.
۴. تفاوت ورق اکستروژن و ریختهگری
ویژگی | اکستروژن | ریختهگری |
---|---|---|
ضخامت | نازک (تا ۶ میلیمتر) | ضخیم (تا ۱۰۰ میلیمتر) |
شفافیت | خوب | عالی (شیشهمانند) |
هزینه | اقتصادی | گرانتر |
مقاومت | مناسب برای مصارف سبک | ایدهآل برای کاربردهای سنگین |
۵. اهمیت فرآیند تولید در کاربرد نهایی
روش تولید تأثیر مستقیمی بر کیفیت ورق پلکسی گلاس دارد:
– ورقهای ریختهگری برای ساخت آکواریوم، ویترینهای لوکس و قطعات صنعتی پراستفاده مناسباند.
– ورقهای اکستروژن برای تابلوهای تبلیغاتی، پوشش نورپردازی و مصارف عمومی کاربرد بیشتری دارند.
—
نتیجه گیری
فرآیند تولید پلکسی گلاس ترکیبی از علم مواد و مهندسی است که به محصول نهایی ویژگیهای منحصر به فردی میبخشد. انتخاب بین روش اکستروژن و ریختهگری به نیاز پروژه، بودجه و الزامات فنی بستگی دارد. با شناخت این فرآیند، میتوان بهترین نوع پلکسی گلاس را برای اهداف تبلیغاتی، صنعتی یا هنری انتخاب کرد.
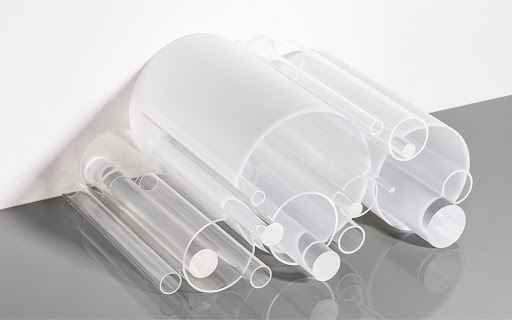
پلکسی گلاس (اکریلیک) نه تنها به شکل ورق، بلکه به صورت لوله و مفتول (میله) نیز تولید میشود. این محصولات به دلیل سبکی، شفافیت و مقاومت شیمیایی، در صنایع مختلفی از روشنایی و پزشکی تا ساخت تجهیزات آزمایشگاهی کاربرد دارند. در این مقاله، به معرفی کامل لوله و مفتول پلکسی گلاس، شیوه تولید، ابعاد، کاربردها و مقایسه قیمت میپردازیم.
—
۱. شیوه تولید لوله و مفتول پلکسی گلاس
فرآیند تولید لوله و مفتول اکریلیک شباهت زیادی به تولید ورق دارد، اما با تفاوت در شکل قالب و مراحل پایانی:
الف. روش اکستروژن (Extrusion)
– مرحله ۱: پلیمر PMMA ذوب شده و تحت فشار از طریق قالبهای استوانهای (برای لوله) یا دایرهای (برای مفتول) عبور داده میشود.
– مرحله ۲: محصول خروجی در حین عبور از دستگاه اکسترودر، به شکل لوله یا مفتول درمیآید و بلافاصله خنک میشود.
– مزایا: تولید سریع، هزینه پایین، مناسب برای مصارف عمومی.
ب. روش ریختهگری (Casting)
– مرحله ۱: مونومر مایع MMA در قالبهای استوانهای یا میلهای ریخته شده و طی فرآیندی آهسته پلیمریزه میشود.
– مرحله ۲: پس از سخت شدن، لوله یا مفتول از قالب جدا شده و پرداخت میشود.
– مزایا: کیفیت نوری بالا، مقاومت مکانیکی بهتر، مناسب برای کاربردهای حساس.
ج. روش ماشینکاری از بلوکهای اکریلیک
– در این روش، لوله یا مفتول از طریق تراشیدن بلوکهای توپر اکریلیک ساخته میشود.
– کاربرد: تولید قطعات با ابعاد بسیار دقیق یا سفارشی.
—
*۲. ابعاد و ضخامت استاندارد**
*الف. لوله پلکسی گلاس**
– قطر خارجی (OD): از ۵mm تا ۵۰۰mm.
– ضخامت دیواره: ۱mm تا ۵۰mm.
– طول استاندارد: ۱ متر، ۲ متر یا ۳ متر (قابل برش به اندازه دلخواه).
– رایجترین سایزها:
– لوله نازک: ۱۰mm قطر خارجی با ضخامت ۱mm (کاربرد در روشنایی).
– لوله صنعتی: ۱۰۰mm قطر خارجی با ضخامت ۵mm (استفاده در سیستمهای تهویه).
ب. مفتول (میله) پلکسی گلاس
– قطر: ۲mm تا ۲۰۰mm.
– طول استاندارد: ۱ متر، ۲ متر یا ۳ متر.
– رایجترین سایزها:
– مفتول نازک: ۵mm قطر (مناسب برای ساخت زیورآلات).
– مفتول ضخیم: ۵۰mm قطر (استفاده در پایههای صنعتی).
—
۳. مقایسه کاربردهای لوله و مفتول
محصول | کاربردهای عمده | مزیت نسبت به فلز/شیشه |
---|---|---|
لوله پلکسی | – سیستمهای روشنایی LED – لولههای آزمایشگاهی – محافظ تجهیزات الکترونیکی |
– سبک و نشکن – عایق الکتریکی – قابلیت خمش حرارتی |
مفتول پلکسی | – ساخت اتصالات دکوراتیو – پایههای نمایشگاهی – صنعت مد و زیورآلات |
– شفافیت بالا – مقاوم در برابر خوردگی – قابلیت رنگپذیری |
—
۴. عوامل تأثیرگذار بر قیمت
– روش تولید: لوله و مفتول کست ۲۰-۵۰% گرانتر از نوع اکسترود هستند.
– ضخامت و قطر: هرچه قطر یا ضخامت بیشتر باشد، قیمت افزایش مییابد.
– رنگ و پوشش: لولههای رنگی یا دارای پوشش ضد UV تا ۳۰% هزینه بیشتری دارند.
– تولید سفارشی: قطعات با ابعاد غیراستاندارد معمولاً ۱۵-۲۵% گرانترند.
مثال قیمتی (تقریبی)
محصول | سایز | قیمت هر متر (تومان) |
---|---|---|
لوله اکسترود شفاف | قطر ۲۰mm، ضخامت ۲mm | ۱۵۰,۰۰۰ |
لوله کست رنگی | قطر ۵۰mm، ضخامت ۵mm | ۴۵۰,۰۰۰ |
مفتول اکسترود شفاف | قطر ۱۰mm | ۸۰,۰۰۰ |
مفتول کست مات | قطر ۳۰mm | ۳۰۰,۰۰۰ |
—
۵. جمعبندی: چرا لوله و مفتول پلکسی گلاس؟
– انعطافپذیری: امکان برش، خمکاری و ماشینکاری آسان.
– مقاومت: تحمل فشار، رطوبت و مواد شیمیایی.
– زیبایی: شفافیت شیشهای و قابلیت افزودن رنگهای جذاب.
اگر به دنبال جایگزینی سبک، ایمن و مقرونبهصرفه برای فلز یا شیشه هستید، لوله و مفتول پلکسی گلاس گزینهای ایدهآل است. برای انتخاب سایز مناسب یا استعلام قیمت دقیق، میتوانید با تیم ما تماس بگیرید.